FBC model – verified by industrial measurements
If model calculations fit well to industry-scale experiments, the established statement can be taken that the model developers understand well the modeled phenomena. This is the case with our overall dynamic model system.
A comprehensive mathematical model for the simulation of both the steady state and dynamic behaviors of circulating fluidized bed combustors will be presented. This model was developed with the special purpose of delivering an effective tool for model-based control design. Because of this aspect, the generation of a numerically highly effective model was a crucial issue. Because of this approach, the model to be presented was permanently undertaken to a critical evaluation regarding all the phenomena to be built in, which in turn resulted in a model built up optimally according to the given preconditions. As the model fulfills them, and as it was successfully verified on measured data as described in the next section, the set of phenomena built-in can be considered as the optimal set describing the real process.
Model verification on dynamical behavior is visible on the next diagrams.
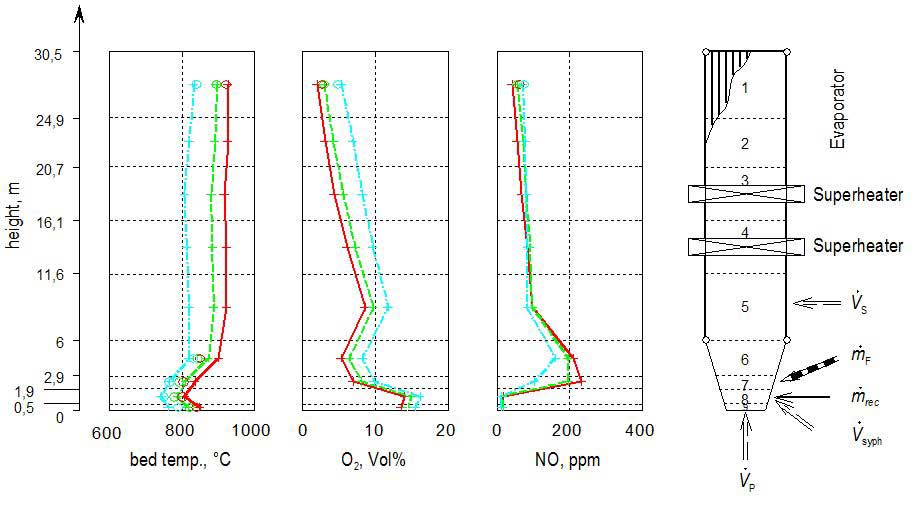
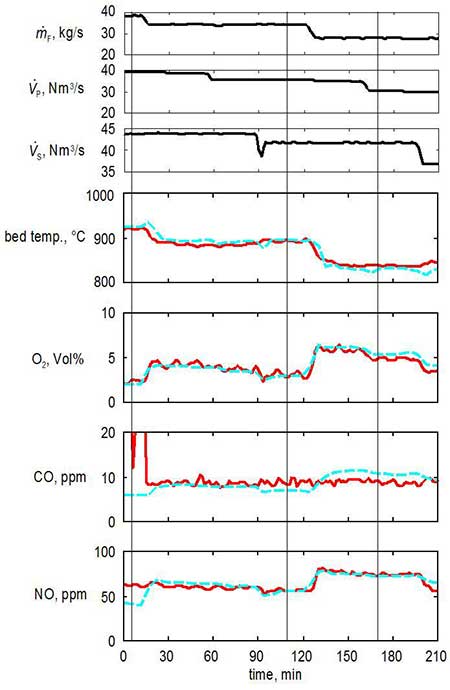
The one-dimensional cell model structure is used, because this approach was found to be very effective regarding computational time on the one hand, and it may consider the dominant spatial inhomogeneity on the other hand. According to this, the combustion chamber is divided into cells along its vertical axis, and these cells are considered as spatially homogeneous ones. Due to the flexible structure of the model, the distribution of the furnace into cells can be chosen freely. The actual used distribution is shown in the next figure.
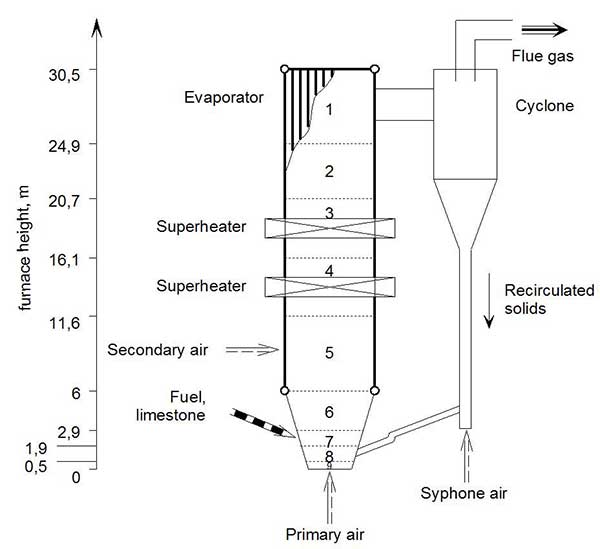
Model measurements can never be understood as the expected data on industry-sized facilities. Similarity numbers must be applied also here. The latest description of this method for FBCs was published in a paper written by two internationally acknowledged professors together with our Dr. Pal Szentannai.
